Revolutionizing the Assessment of Carbon Footprint in Ammonium Nitrate and Fuel Oil Explosive Detonations
Introduction
The global focus on addressing environmental challenges has intensified, with significant attention on reducing greenhouse gas emissions, mitigating resource depletion, and combating environmental pollution.
To tackle these issues, countries worldwide are actively engaging in efforts to mitigate climate change. This involves making commitments to emission reduction and adopting advanced technologies to limit greenhouse gas emissions.The carbon footprint originated from the concept of the ecological footprint, which was introduced by Wackernagel and Rees in 1998 . The ecological footprint measures the total land and water area needed to produce resources and handle waste linked to the consumption of individuals, organizations, products, or countries. The carbon footprint, following a similar principle, measures the mass of CO2 emissions instead of land area (Figure 1).
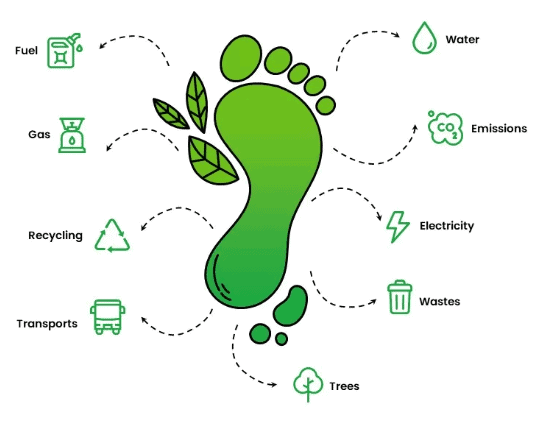
In drill and blast operations, the main sources of emissions are the use of explosives and fuels. These emissions are directly generated during the detonation and combustion processes.
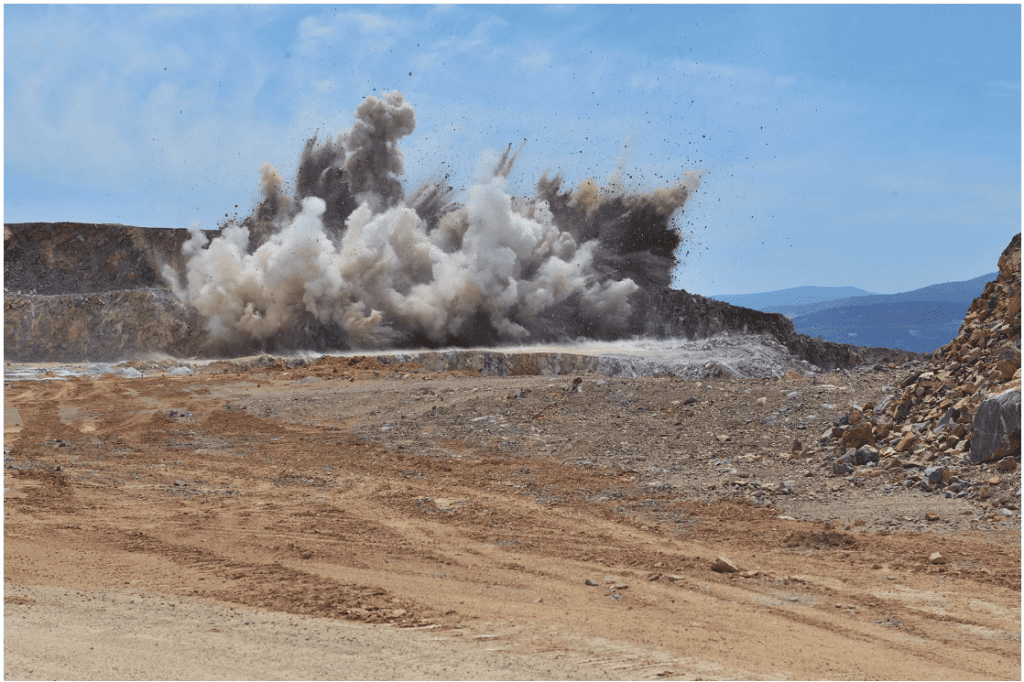
Ammonium Nitrate and Fuel Oil Explosives Carbon Emissions
The explosion reaction can be described as a rapid oxidation-reduction process involving a fuel and an oxidizing agent. In this exothermic reaction (1), the fuel undergoes oxidation while the oxidizing agent undergoes reduction, resulting in the release of energy in the form of heat (Q). In an ideal scenario with sufficient oxygen, the reaction is considered balanced, where all the hydrogen (H), water (H2O), and carbon (C) are oxidized to form carbon dioxide (CO2). Nitrogen (N) is regarded as inert and contributes solely to the formation of dinitrogen or nitrogen gas (N2).

Calculating the CO2 emission factor for ammonium nitrate and fuel oil explosives involves determining the amount of carbon dioxide emitted per unit of explosive used. This process considers the carbon content of each component, as well as their combustion efficiency. First, the carbon content of ammonium nitrate and fuel oil is determined. Then, the respective amounts of these components in the explosive formulation are considered. By applying the combustion efficiency factor, which represents the extent to which the carbon is converted into carbon dioxide during the explosion, the CO2 emission factor is calculated (Figure 3).
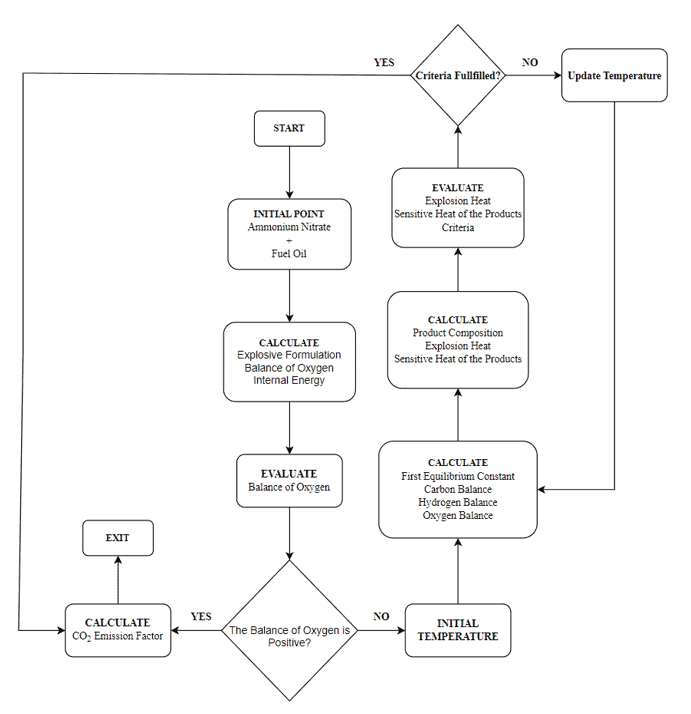
Blast Design and ANFO Carbon Emissions
Blast design is a crucial aspect of various industries, particularly mining, quarrying, and construction, where controlled explosions are employed to extract minerals, break rocks, or create foundations (Figure 4). It involves the meticulous planning and engineering of explosives to achieve desired outcomes while ensuring safety and minimizing environmental impact. Blast design encompasses several key elements, such as determining the optimal explosive type and quantity, designing the blast pattern and drilling layout, considering rock properties and geotechnical conditions, and assessing potential risks and vibrations. A well-executed blast design aims to maximize productivity by optimizing fragmentation, minimize energy wastage, and reduce the potential for flyrock, ground vibrations, and air overpressure.
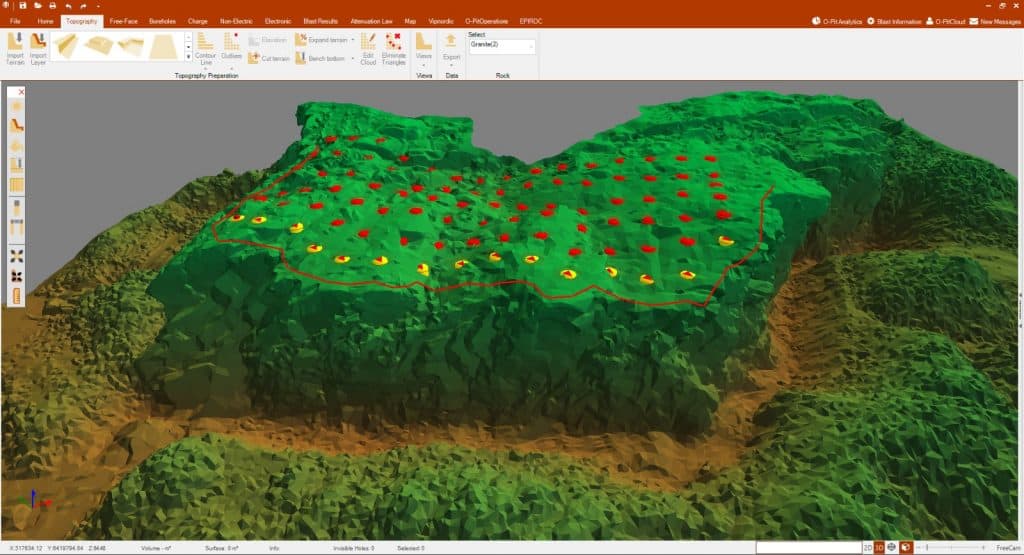
O-PitSurface proves to be an excellent tool for this purpose, as it offers a comprehensive simulation feature specifically designed to manage, measure, design, and evaluate all aspects of the blast cycle.
For the ideal ANFO, 94.5% of Ammonium Nitrate and 5.5% Fuel Oil when applied previous calculation we can get a CO2 Emission Factor of 0.150 kg CO2/kg explosive.
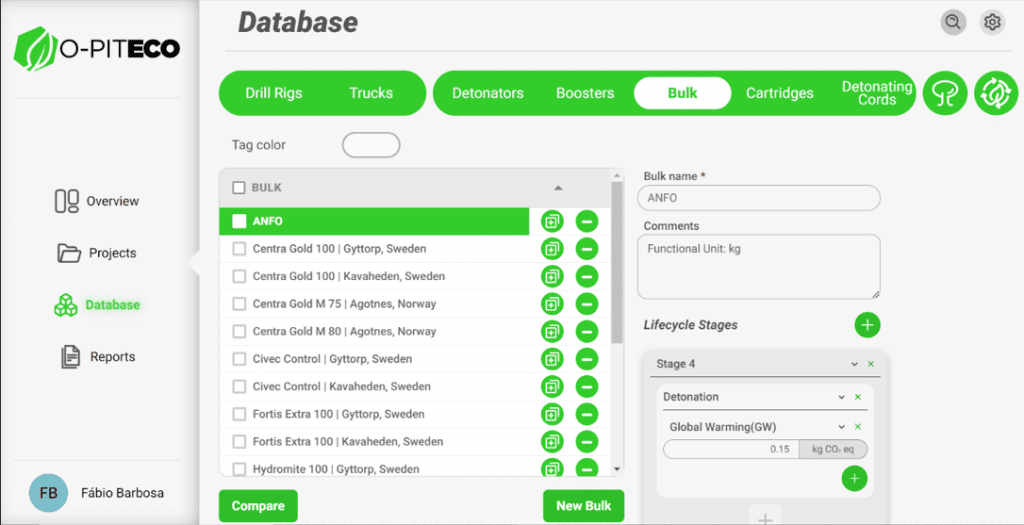
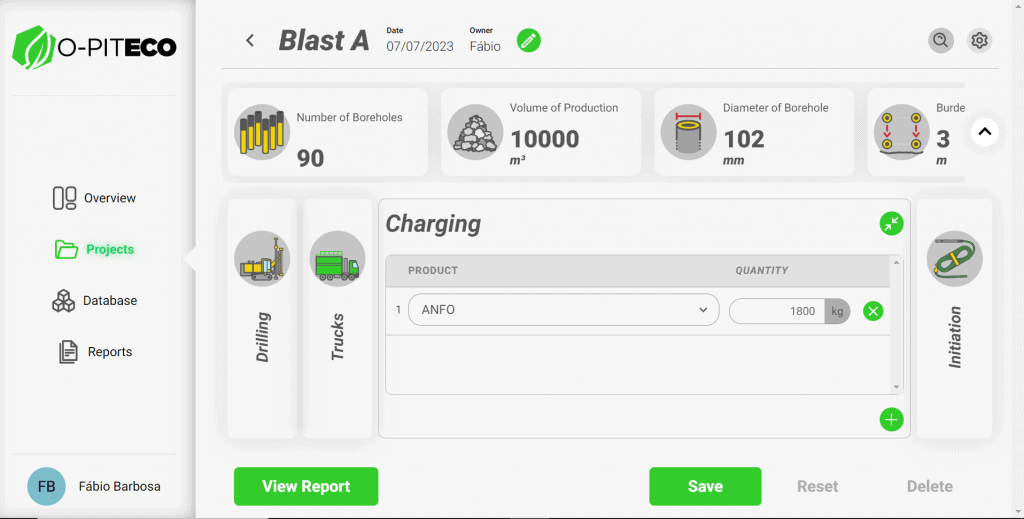
Considering the blast with 90 holes and 20 kg per hole, it attends a total of 1800 kg of explosive and 270 kg of CO2.
O-PitEco proved to be a valuable tool for this study due to its advanced computational capabilities, which were utilized to accurately estimate the emission factors associated with drill and blast operations.