Introduction
When the subject is related to mining and blasting, precision and safety are of supreme importance. One key factor that plays a critical role in achieving both is the stemming
Stemming control refers to the careful management of the height and density of stemming material used in blasting operations. This seemingly small detail can have a significant impact on the efficiency and safety of mining and blasting operations.
Stemming material, typically made of crushed rocks or other inert materials, is used to confine the explosive energy generated during blasting. It is placed in the boreholes above the explosives to prevent them from prematurely escaping through the blast hole, thereby maximizing the energy transfer to the rock mass (Figure 1).
Proper stemming control ensures that the explosives are contained within the blast hole, leading to optimal fragmentation of the rock and minimizing flyrock (Video 1) , ground vibrations, and airblast.
Key factors for stemming control
So, the question that we will dig into in this blog is: how do I choose the best-stemming control for my operations? Let’s dive into some of the key factors to consider.
- Stemming Material: The choice of stemming material depends on various factors such as the type of rock or material being blasted, the size of the drill holes, and the desired fragmentation outcome. Common stemming materials include crushed rock, sand, clay, and specialized products like expanded perlite or foam stemming.
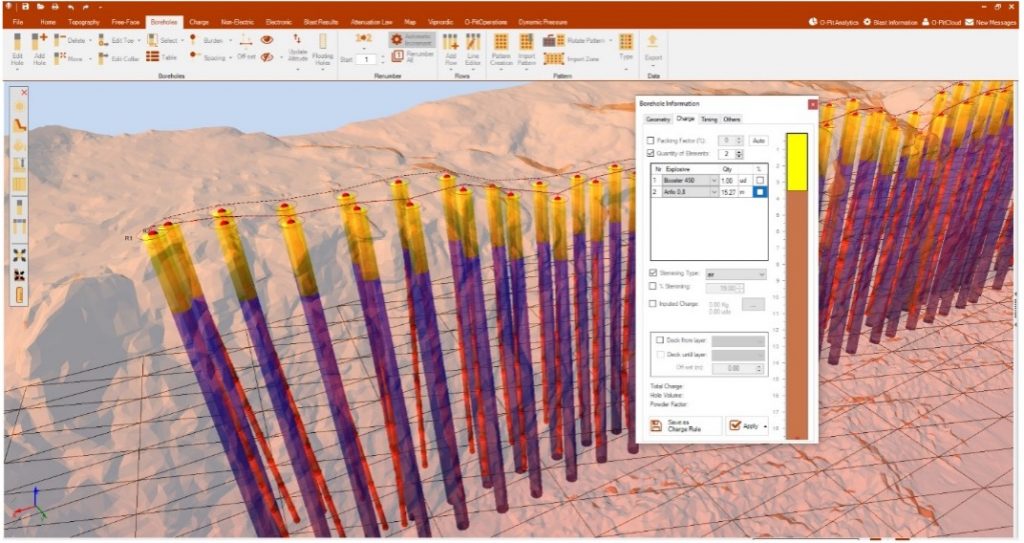
2. Stemming Length: The length of the stemming material is crucial in controlling the blast energy. Too short stemming may result in energy loss and inadequate confinement, leading to poor fragmentation and flyrock. On the other hand, overly long stemming may result in insufficient energy release, leading to inefficient blasting and increased operational costs. There are tools available such as the O-PitBlasting Guide app (Figure 4) that can assist you in calculating the optimal stemming height and particle size.
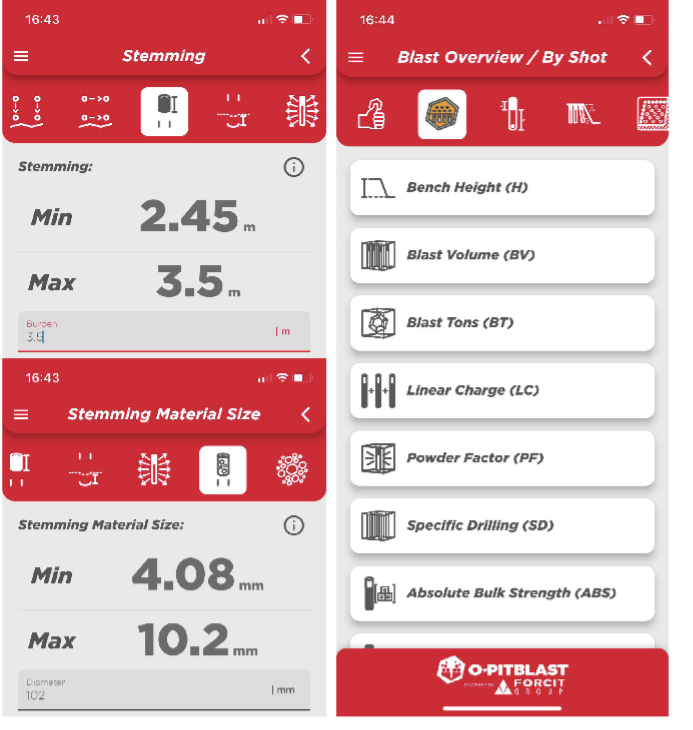
3. Stemming Uniformity: Ensuring uniformity in the stemming material is essential for consistent blasting results. Irregularities such as voids or gaps, can result in uneven confinement of explosive energy, leading to uneven fragmentation and reduced blast efficiency. Proper placement and compaction of the stemming material should be ensured to maintain uniformity and achieve optimal blasting outcomes (Figure 4).
Formulas and best practices
Below are practical formulas and tips that can be used to calculate particle size and stemming height.
1. The particle size should be such that it can effectively fill the void spaces in the blast hole and provide confinement – Diameter / (10 to 25) (Figure 5)
2. The height of the stemming material should be sufficient to prevent gas leakage and allow for efficient energy transfer – (0.7 to 1) X Burden (Figure 5)
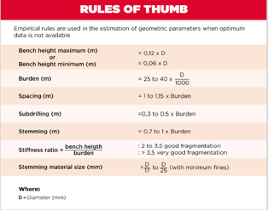
3. Evaluate the cost and availability of the stemming material. The stemming material should be cost-effective and readily available for use.
4. Monitor the blast results and adjust the stemming material as needed to improve blast efficiency and fragmentation.
Conclusion
Stemming control is a critical aspect of mining and blasting operations that should not be overlooked. It requires careful consideration of stemming height and density to achieve optimal blasting results while ensuring safety. Site-specific assessments, monitoring, and adjustments during blasting operations are necessary to achieve the desired stemming control. By paying attention to this seemingly small detail, mining and blasting operations can achieve better fragmentation, improved safety, and increased efficiency.
I hope this information could be useful in your daily work!
See you all soon!