Back to Basic
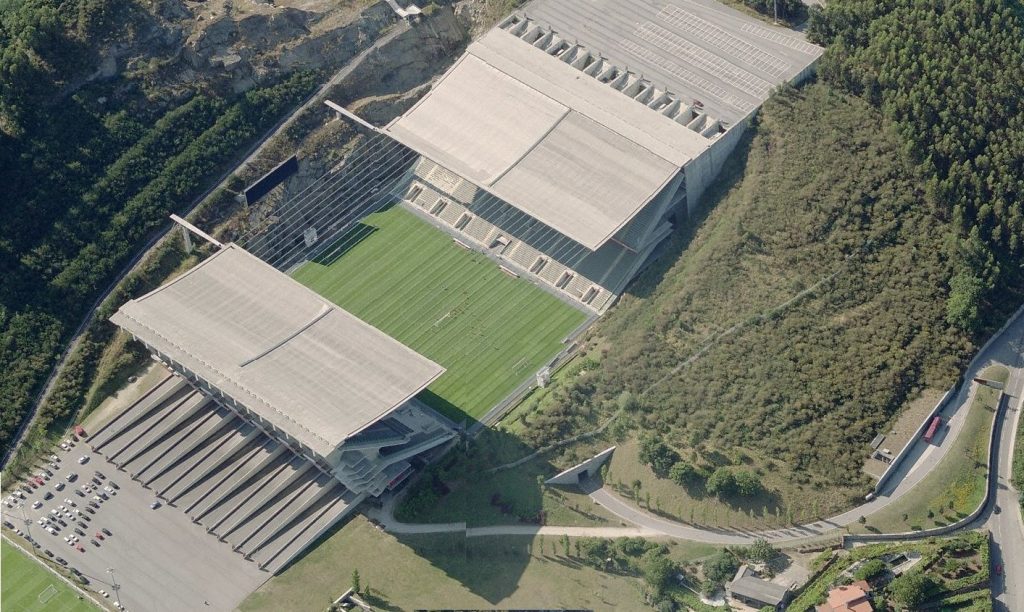
Normally mining operations tend to proceed with practices that at a given moment have led to satisfactory results, a popular saying that if something is good, do not change it, it is well known and applied especially in quarries, where there is usually a certain resistance to the implementation of new technologies and changes in daily practices.
figure 1 – S.C. Braga stadium in a quarry)
It is common, just to give an example, that as a quarry develops over the years the nearby population also evolves and in certain cases it approaches its limits of exploration. Situations like this are common and become sources of disputes, on one hand the quarry needs to maintain its production in order to be economically viable, and on the other hand, the neighbouring communityis pressing for lower levels of environmental impacts, especially dust, noises and vibrations, both those originating from the rock blasting activity, and those induced by heavy machinery, and absolutely zero risk of accidents related to fly rocks.
In order to adapt to these restrictions, thus remaining both economically and environmentally sustainable, it is advisable that managers and engineers, key players in decision-making, to maintain an open attitude towards new technologies and, in a way, make a return to basics, in others words, aspects related to productivity should be resized as much as possible, in such a way as to minimize environmental impact and promote the high efficiency of the extractive chain.
Thus, in this way, quarry benches need to be resized in function of the excavation and transport equipment, very high benches can lead to an increase in drilling deviations, poor fragmentation and higher levels of vibration, fly rocks and boulders when blasting. A poor choice ofdrilling pattern also causes several problems related to fragmentation, which in turn reduce the efficiency of the loading and transport process, and finally, the efficiency of the crushing equipmentis affected by constant stoppages due to jaw jamming. A higher level of wear on loading and transport equipment and crusher is also expected due to excessively coarse and irregular fragmentation. Blocks of rock whose dimensions are not possible to be transported or processed are usually left aside and later require secondary blasting, which increases the risk of accidents dueto rock projections or the hiring of equipment capable of breaking these rocks without the use of explosives. All these factors, when added together, increase the operating costs of the production chain.
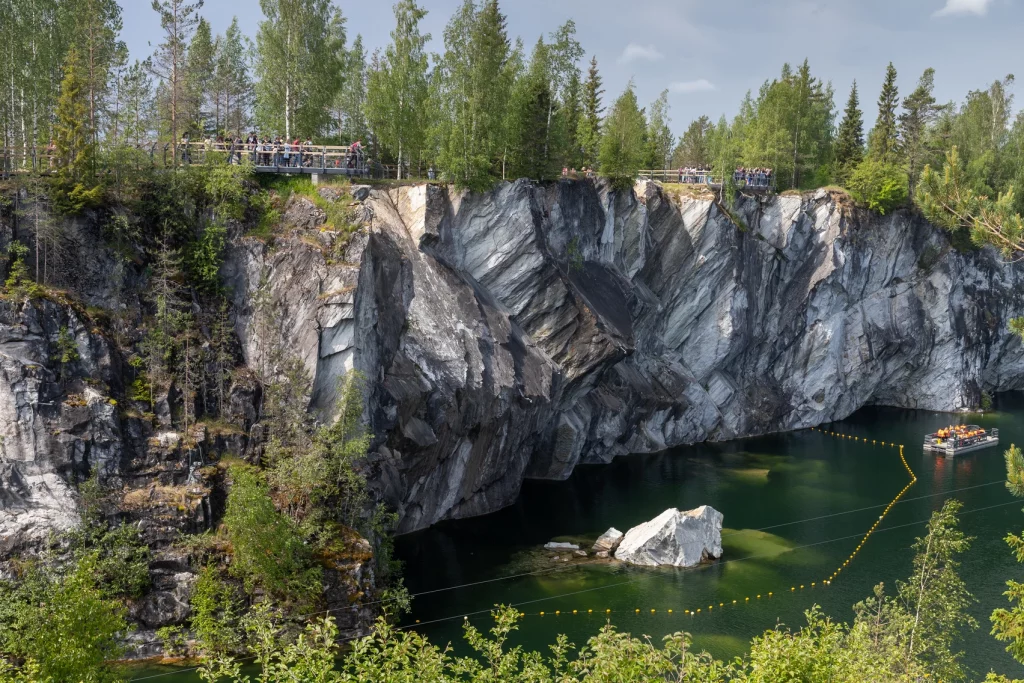
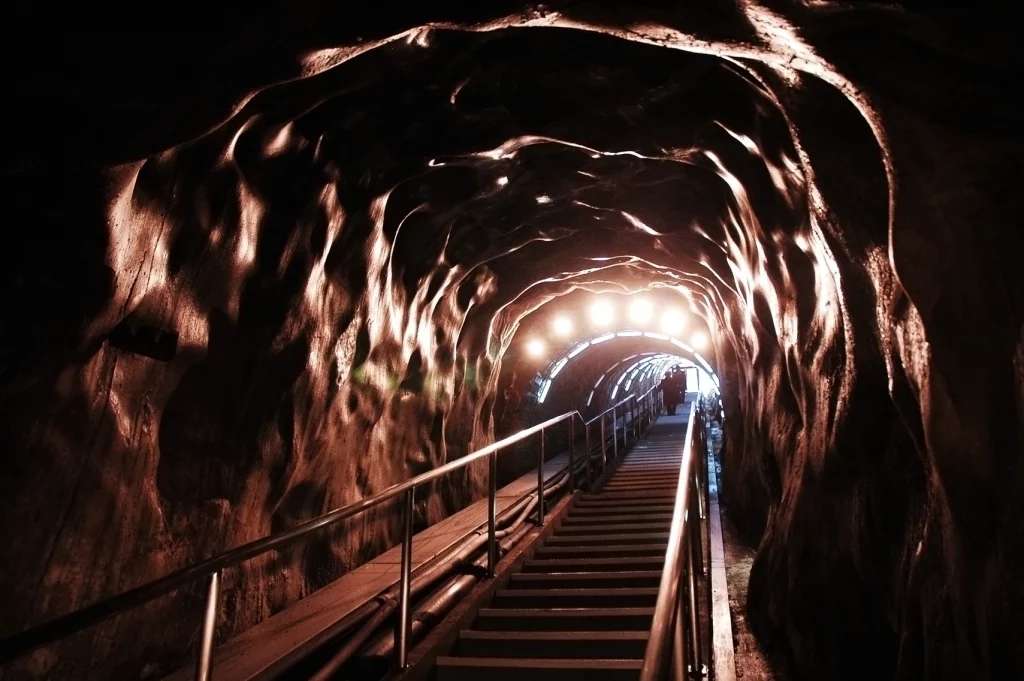
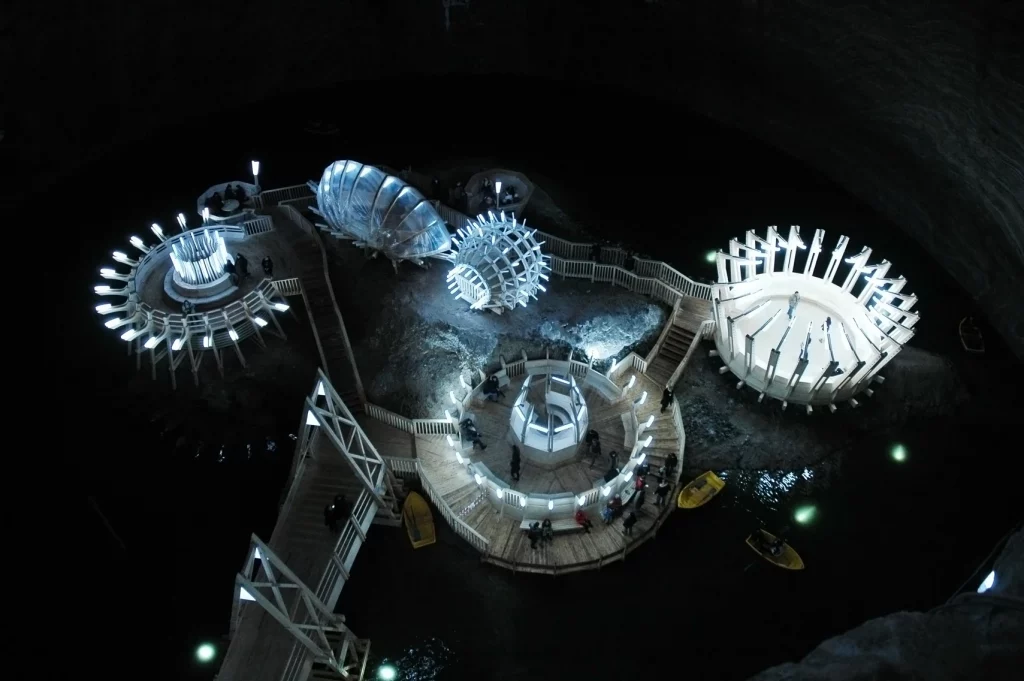
An efficient way to return to the basic design and determine the optimal mesh capable of promoting the reduction of operating costs and minimising the risk of projections is the use of state-of-the-art technologies to design the blasting plan and audit the drilling mesh, allowing corrections in holes before explosive charging and blasting.
For an efficient dimensioning of benches, safety aspects, geotechnics information, loading and transport equipment, drilling diameters and general blasting objectives must be taken into account. Predictive fragmentation models can be used in this sense, since they combine the available information, in terms of bench geometry and its geotechnical characteristics. The type of explosive used and its spatial distribution in the bench through the drilling pattern. All these inputs will be used to estimate the fragmentation that is most efficient to attend granulometric requirements to further steps on the production chain.
Efficient Blasting
Once the blasting objectives are established, it is necessary to carry out a topographic survey of the bench to be blasted, this is important for a perfect positioning of holes in a row and specially to reduce the risk of fly rock caused by holes close to weak points on the free face. 2D/3D lasers have been used for this purpose, however drones provide an advantage over this equipment, as their acquisition cost is generally more attractive and drone operator can safely do the surveying without expose himself to harms or disturb operation on the pit, also the speed of operation is lesstime consuming with a drone when compared to lasers alternatives.
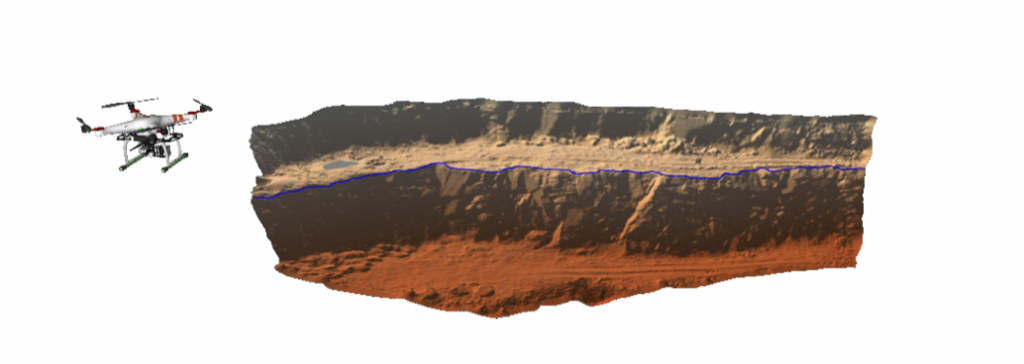
After the terrain survey is done, it needs to be exported to a software capable of favour the decision-making process when designing a blasting plan. O-Pitblast Software provides a whole range of “built in” solutions that help the engineer or technician responsible for the blast to achievethe best possible result, taking into account safety and productivity criteria. The O-Pitblast softwareallows you to simulate load and firing sequence, critical distances for fly rocks, expected fragmentation, vibration levels, and the costs associated with blasting.
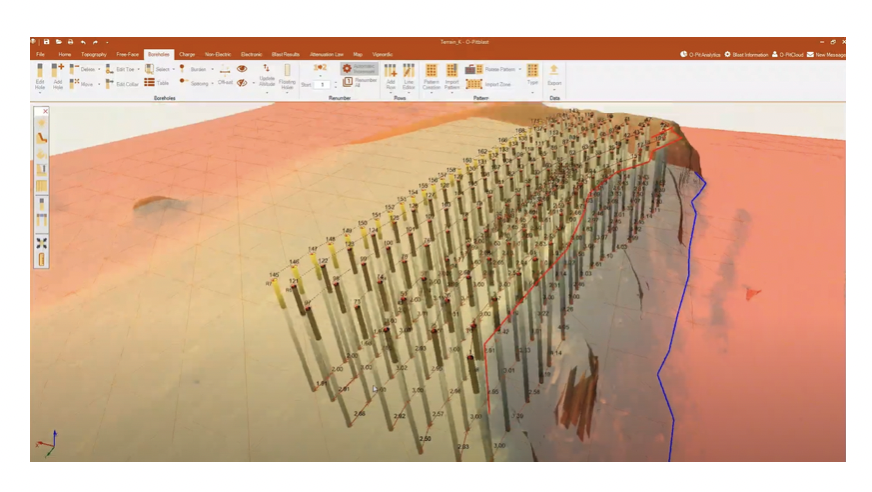
It is important that once the drilling is carried out, it is audited. There are several problems related to poor drilling and therefore, it is always necessary to ensure that the drilling is as good as what was planned, so the correct positioning of the holes, their length and inclination must be as reliable as possible to ensure an efficient blasting.
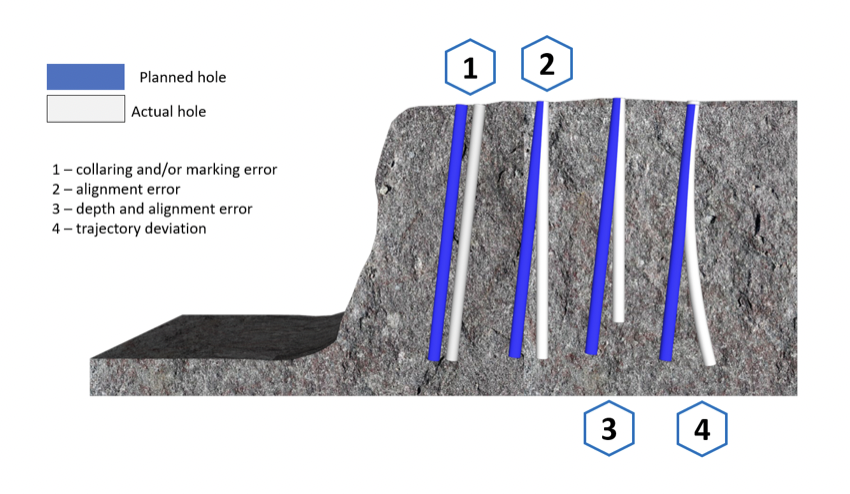
Hole length and inclination can be controlled with O-PitDev, this device allows you to simply and quickly gauge holes and generate reports in real time with an application specially designed forthis purpose.
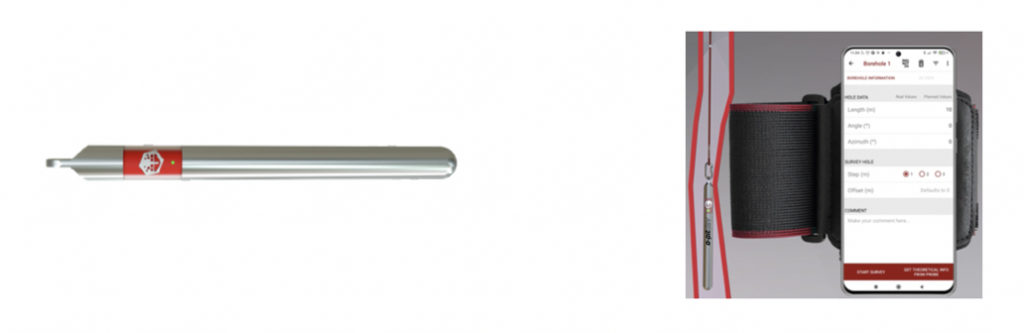
In this way, a return to basic design parameters, taking advantage of what technology can offer, allows quarries to keep its production sustainably, profitable and safety to nearby communities with the minimum level of environmental impact generated.
How much it cost to have such state of art technologies on your quarry?
Not much really, in fact it is an affordable solution.
To find out more, contact us and don’t miss the next articles on this topic.