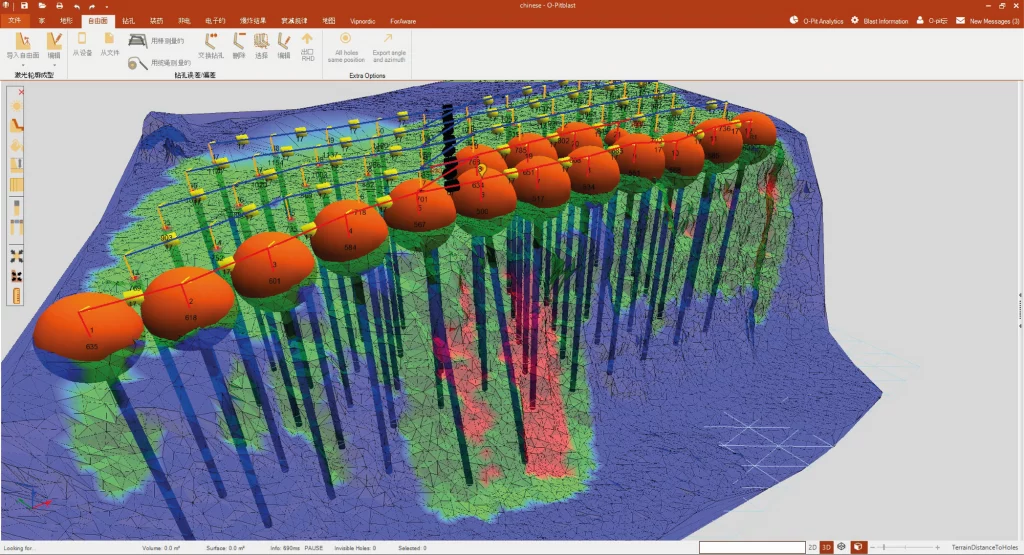
New technologies aimed at minimizing costs in mining sector is the focus of our article. This article aims to present some methods used to optimize the drilling and blasting process in a certain aggregate company, aiming at optimizing the process, generating a reduction in costs with blasting (both primary and secondary), consequently increasing the useful life of loading, transport and crushing equipment.
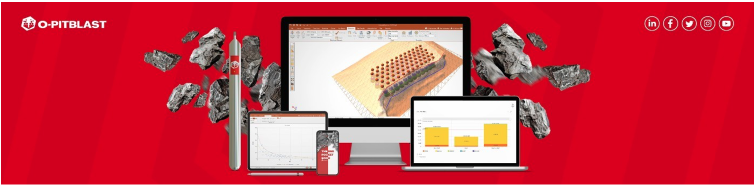
Rock drilling is the first stage of mining and all other subsequent operations such as blasting, loading, transporting and crushing depend on it. Thus, the optimization of drilling contributes to cost reduction of next phases.
Factors that will influence the blasting parameters should be taken into account when planning, such as: volume of rock required, in terms of daily, weekly and monthly production, type of drilling equipment and available drill bits, size of loading and haul trucks, expected fragmentation and gap of primary crusher.
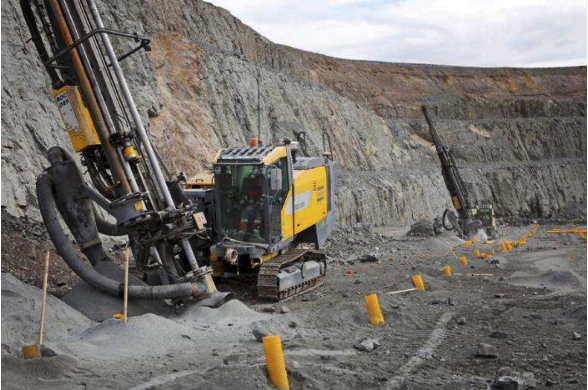
A decisive factor to perform a blasting without the occurrence of flyrock and also
to reduce unnecessary explosive consumption is the full knowledge of the free face of the bench to be blasted, for this, it is recommended the use of laser technology, drones and inclinometers that allow us
to visualize on the computer the volume to be blasted, accurately determine the profile
of the rock face, determine the direction
and depth of the holes, recalculate explosive loads based on actual hole position, among other features.
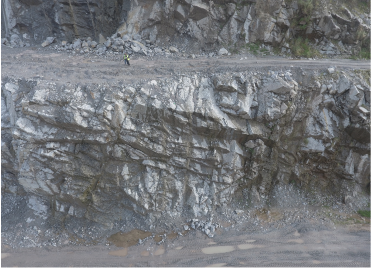
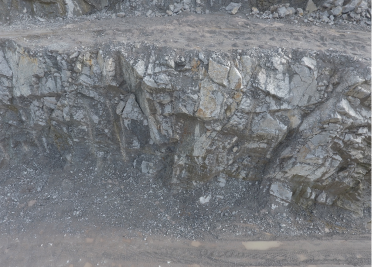
When drilling, the holes must be as straight as possible, aiming at the correct distribution of explosives and the reduction of flyrocks. The results, in terms of fragmentation, must be compatible with the loading (Modernising material handling in the mining industry | Engineer Live), transport equipment and crusher to avoid secondary blasting.
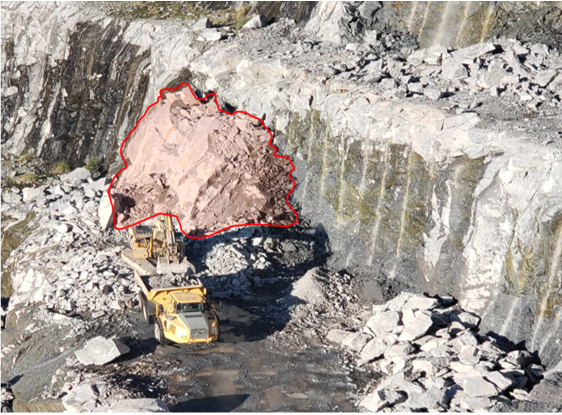
Blasting – Technical considerations
From the information provided by the technical team of the company under study, the blasting parameters can be outlined as shown in the figure below.
In short:
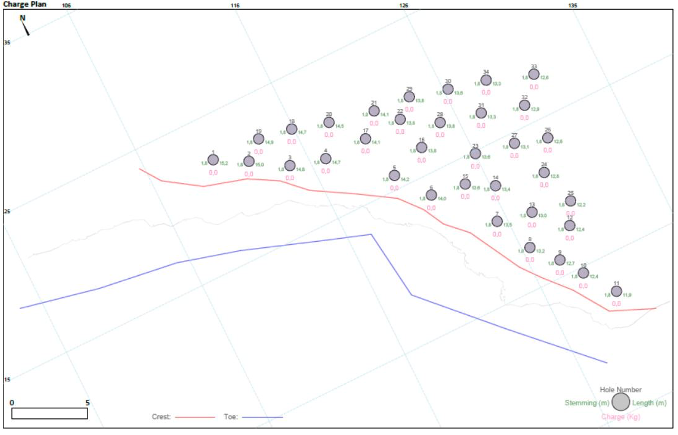
• Burden (A): 2.7m
• Spacing (E): 3.0m
• Average depth of holes (H): 18m
• Hole Diameter (Ø): 76mm (3 inches)
• Predicted slope: 12th degrees
Stay tuned for the final part of Thales article…