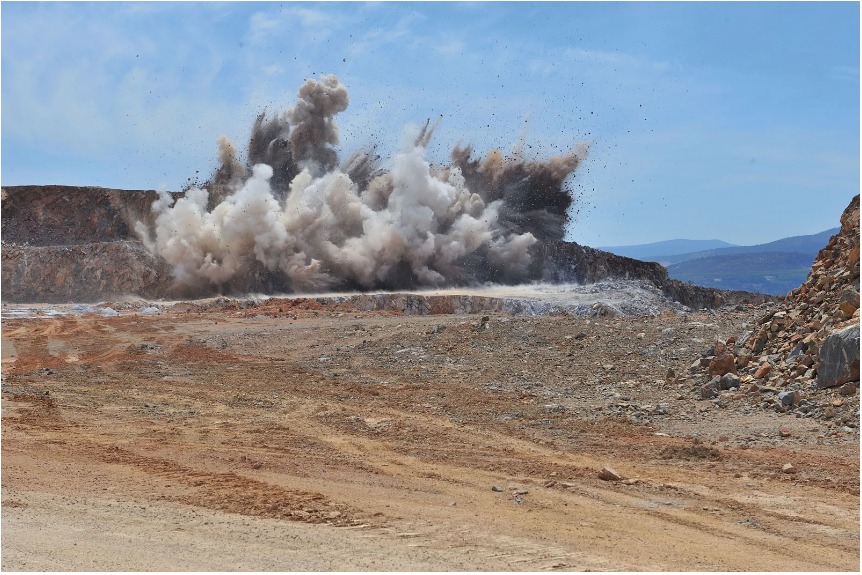
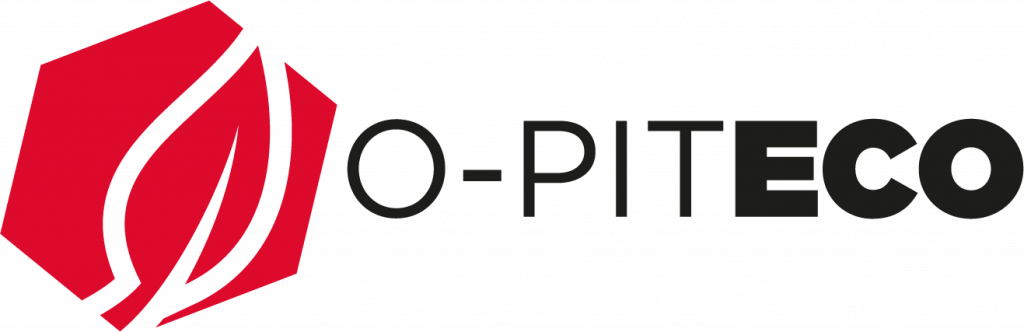
International agreements influence governments to pressure companies to adopt measures to manage their environmental impacts. The activities of the extractive industry have numerous impacts on the environment, for example, the gaseous emissions emitted, the rejected materials, or the drainage of acids contained in the effluents from the mine. It is then expected that companies operating in the extractive activity sector, establish measures and adopt policies that allow for reducing their damage to the environment, simultaneously with profitable economic development. Digitization is one of the biggest vectors of change in the industrial sector, particularly in the mining sector. The productivity and sustainability of drilling and blasting operations can be dramatically increased using digital optimization tools. It is also possible to reduce non-detonating boreholes, which indicates savings at economic levels and subsequently increases the sustainability of the various projects. Thus, it becomes logical to develop a model that can calculate and evaluate emissions, in particular CO2 emissions from drilling and blasting operations.
Emissions in a breakdown
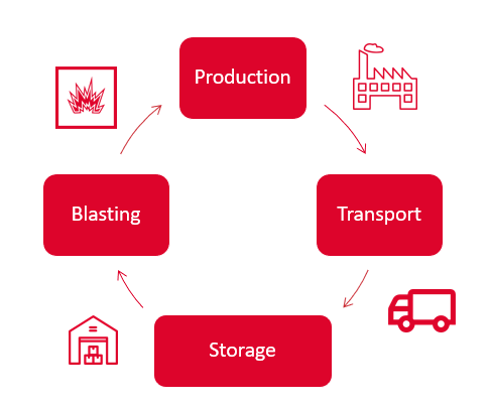
Gaseous emissions associated with blasting using explosives (Eexp) are mainly due to the use of the latter as a whole (Mexp) and their respective emission factor (FEexp) and can be described, globally, by the expression:

The expression that allows the calculation of the emission factor for explosives, considering direct (Detonation – FEexpD) and indirect (Production – FEexpP; Transport – FEexpT and Installation – FEexpI) emissions are:

The emission factors for indirect emissions are provided by Life Cycle Analysis (LCA) technology. In turn, direct emissions can be given by the analysis of experimental results or by prediction models of gaseous products resulting from detonation.
The model for reducing Emissions in a blast
It started by creating a database with all the emission factors, as well as all the properties of the explosives, associated with the categories of environmental impact, from an LCA perspective. The model (Figure 3) requires the user to indicate,first, the volume to be dismantled, the average hole diameter, the height of the bench, the desired fragmentation, a first draft of the firing diagram and the selection of the explosive to be used, within those registered in the database. Next, we begin by calculating the average length of each hole, the average volume of each hole, the number of holes, the mass of explosive per hole and the total mass of the explosive, as well as parameters related to fragmentation.
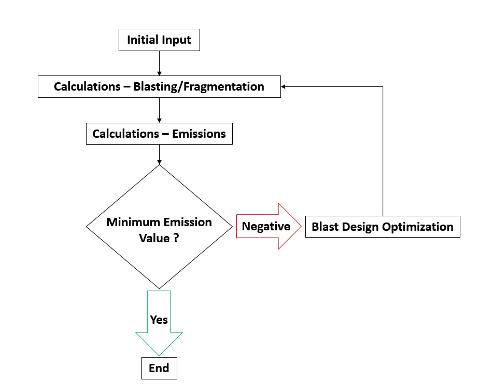
If the emissions value is the minimum, within the constraints of the fire diagram and fragmentation, the model ends the calculations. Otherwise, using the Generalized Reduced Gradient (GRG) optimization method, the model will find the solution for the firing diagram, changing its variables, to reach the lowest emission value. The life cycle analysis applied to explosives provides, among others, values for emissions related to their detonation and transport, as well as values applied to environmental impact categories. Thus, in this way, it was possible to successfully conclude the presentation of a model for controlling emissions in dismantling operations. In the following video, it is possible to see, briefly, why the control of environmental impacts in extractive industry operations is so important.